
(
photo from the Villin website)
I was browsing craigslist for bikes and ran across a "locally made" Villin fixie for $1200 "originally $1700". "Hmmm," says I. "What is this shop called Villin?" So, I googled Villin and found
http://www.villincycleworks.com/ I read Villin's philosophy: "Consider purpose. Since the industrial revolution, workers have been given less and less reason for people to care about their craft no matter what it is. The classic quote from Office Space summed it up "I work just hard enough to not get fired" It really was beautiful. The irony of a whole era. Such a monumental loss of purpose for so long that it changed the definition of purpose itself." This is where the adventure began...
Several things about the Villin site drew me in. There's a definite focus on the craft of frame making. Villin's photo gallery is full of pictures of hand made components in various stages of construction. The whole site has an artisan feel. And, a suggestion to drop by and check the shop out. So, I called Villin owner Alexis "Lex" Dold to see when it might be convenient to drop by.
Somehow, the voice that answered the phone didn't match my expectation of what I'd hear after browsing Villin's edgy site and the photo of Lex, smoking a cigar on the front porch of his house. I imagined a double-barrel shotgun leaned up against the cedar shake, out of site... On the contrary, Lex's voice was cheerful, inviting and friendly. He basically said "Ya know where
Satchel's pizza is? I'm just around the corner. When ya comin' by?"

(
Click the photo above to see the entire set related to this article)
The Villin website suggest bringing your bike by so Lex could see what you were used to riding. So, I loaded up my Miele Volta and the Dawes Galaxy and headed out. When I arrived at Villin, Lex walked out to greet me holding a custom wheel he'd been polishing.
We said howdy, shook and he invited me into Villin Cycle Works. I heard electric guitar music wafting out the warehouse door, playing from some clean speakers. My eyes immediately went to a bike trailer with a cooler affixed to it. Lex offered no immediate explanation aside from something like "It's for Artie. You'll meet him shortly".
Right next to the trailer was a table saw with a beautiful piece of wood on it. Lex said he also liked working with wood.
Lex said "Have you ever seen any raw materials for bikes?" pointing to a box full of tubing. He explained that the materials he used at Villin were top shelf and showed me the tubes. I felt the unfinished, raw metal tubing and imagined how many steps might be taken to arrive at the finished product.

Lex pointed to a frame above the raw tubing. He described some of the signature aspects of the Villin frames. The custom lugs, the curved seat stays, and other subtle features.

We stood near a vintage looking green touring bike. It had a paint job that had a luster unlike most new bikes you'd see in a shop. Lex had a smile on his face only someone very proud of his work could have. The seat was a leather saddle, Brooks style. Green's my favorite color. I love touring bikes. I was in trouble...

I took a closer look at the bike.
I really liked it.
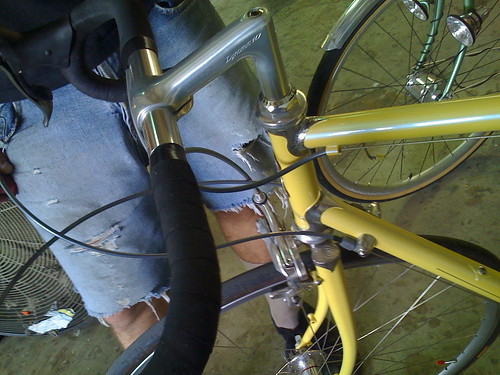
Lex pointed to another finished bike's lugwork. This lugwork was an aspect of Villin cycles he was particularly proud of.
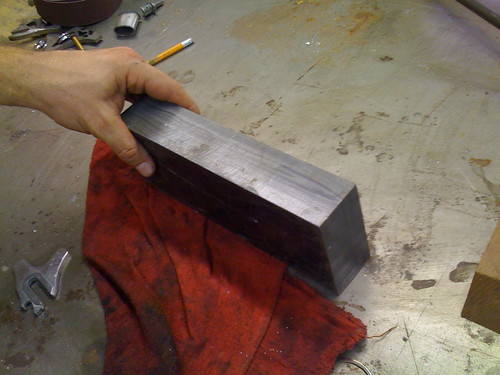
Lex asked me "Have you ever seen anything like this steel? It's the same kind used in Samari swords." Pressed steel, I think he said.
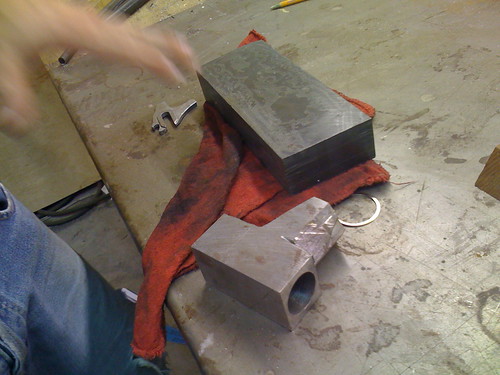
Lex then said "Take a look at this lug. You can see that I take the pressed steel and that's where the strength of the custom lug begins."

Then, we looked at a frame that had just been welded together. I thought back to my metal shop days in school and admired the brazing work he'd done.

Lex showed me how he fashioned forks from the raw materials.
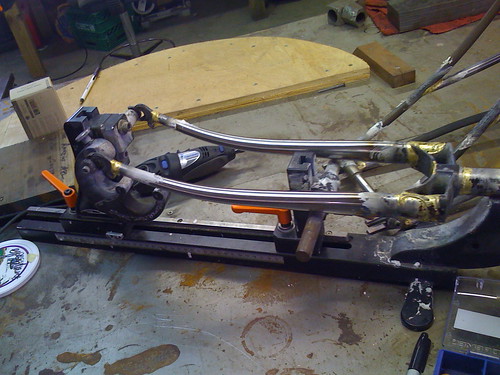
There were specific tools used for the forks and most of the other components along the way to the finished product.
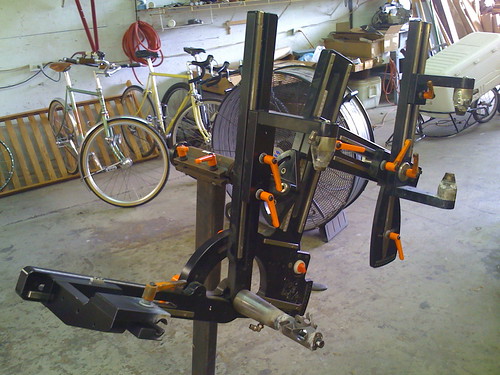
Lex was particularly proud of the frame brace you see above.
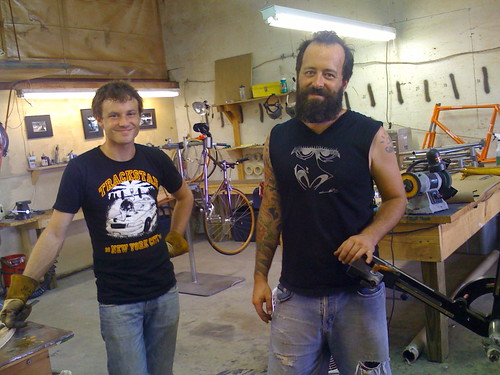
Lex runs Villin like a tight ship. Here you see Lex with his assistant, Joe. He requires a $500 deposit to put your name on his waiting list. The time to delivery is 16 months.
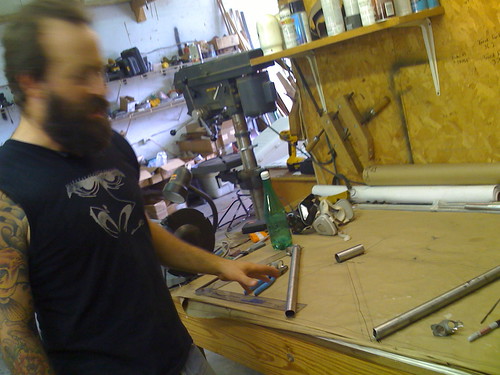
We walked over to the drafting board and looked at how a frame geometry was translated from drawing to actual product.

It became very clear that the measurements translated to real angles on paper. These mockups then act as layouts for the actual frame. Lex takes a great deal of time making measurements. The measurement session includes a ride on a bike to see how you move. Then, as you'll see in coming photos, Lex makes many measurements that determine best fit for the individual.
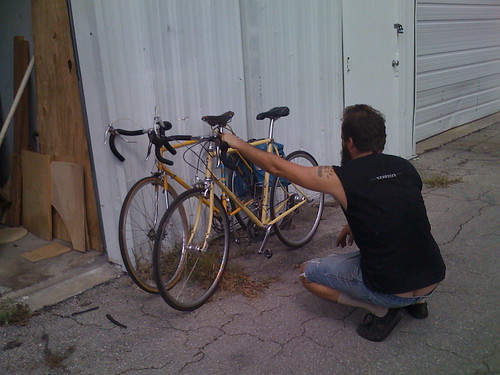
Here you can see Lex examining my yellow Dawes Galaxy. I've been riding it a long time and Lex wanted to see what I was used to.

Precise measurements of my Dawes Galaxy gave Lex a good starting point for the design of my potential new frame.
The "pot" in the photo above is what Lex calls his Fluxinator. It's basically a pot of boiling water to dissolve flux. It's one of many smart innovations Lex has designed in his years of frame making.

Lex paused in the tour and just explained to me how he loves his work. He loves creating a fine piece of usable machinery.
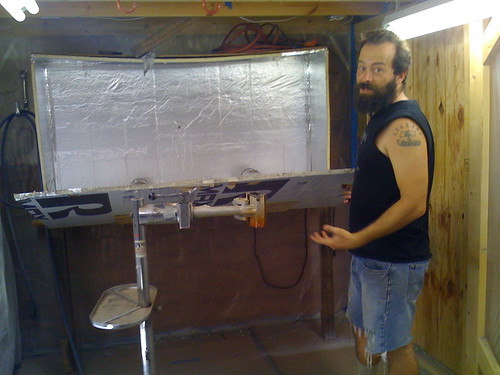
Next stop on the Villin tour was the paint shop. Here, you can see where the paint is baked on the frame.

Lex's shop Villin is right next to a local artist's warehuse. The area Lex uses to paint his bikes has some gratuitous artwork.

Villin also makes off road bikes. The bike above is an excellent example.
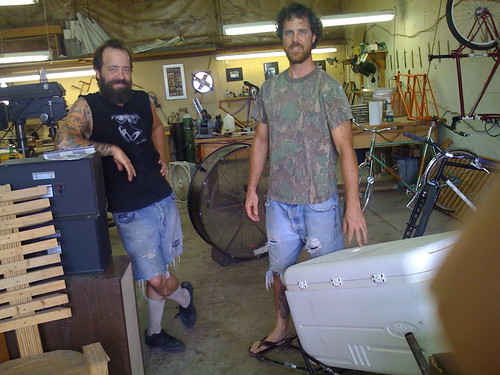
Artie Guy of
Artie's Tempeh, a local artisan tempeh purveyer here in Gainesville (in case you haven't heard of him!) dropped by to pick up his trailer. Now, Artie can deliver his tempeh the natural way!
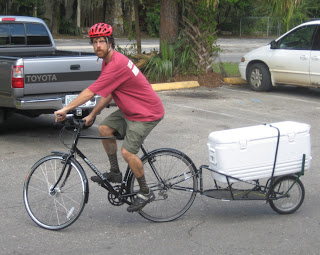
(
photo from www.artiestempeh.blogspot.com/)
"Green as it gets. Delivering now by bicycle"

Moments later, Gus Woodruff from Gainesville's
Mr. Goodbike, a long time and beloved local bike shop near University of Florida dropped by. I was feeling more comfortable by the moment, knowing I was in the company of some of Gainesville's "Green Cognoscenti".
So, a good time was had by all. I walked away knowing a lot more about bicycle frame making in general and Villin's artisan approach specifically. Thumbs up!